New Standards under the Consumer Product Safety Improvement Act Come into Force
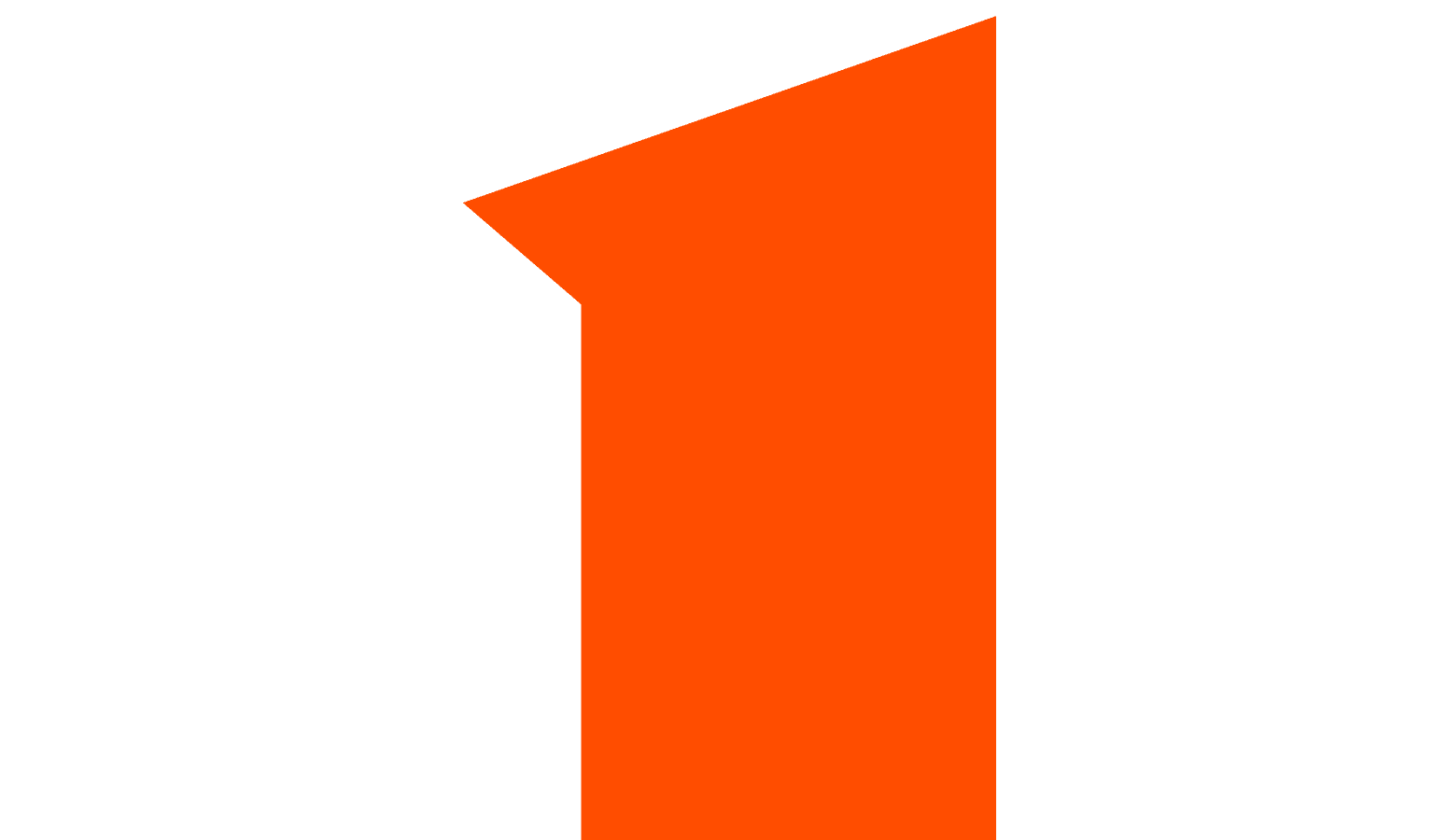
On February 10, 2008, new standards came into effect under the Consumer Product Safety Improvement Act (CPSIA).[1] These criteria set limits on lead and phthalate levels in children’s products (designed or intended for use primarily by children 12 years old or younger)[2] and establish mandatory standards for toys. The Consumer Product Safety Commission (CPSC) recently decided to stay the enforcement of testing and certification requirements related to these particular standards for one year to give manufacturers (including importers)[3] sufficient time to comply with these procedures.[4] Nonetheless, the underlying safety standards are still enforceable on manufacturers, importers, private labelers and retailers.[5] Therefore, it is essential that importers and other regulated parties design appropriate compliance strategies.
Overview of the Law
The CPSIA, which became law on August 14, 2008, places significant restrictions on certain importers. The law strengthens rules on certain consumer products and creates new testing, certification and tracking requirements. The CPSIA also increases enforcement efforts and the potential penalties for violations. These new rules apply to some extent to all parties in the import supply chain, including manufacturers, importers, private labelers and retailers.
Product-Specific Restrictions
The law contains various heightened restrictions and bans on certain products and product characteristics. Among them are—
- A lead ban on children’s products . Section 101 of the law progressively decreases the permitted amount of lead in children’s products. As of February 10, 2009, no product may have more than 600 parts per million (ppm). On August 14, 2009, the level lowers to 300 ppm. Finally, on August 14, 2011, the limit becomes 100 ppm, unless such quantity is not technologically feasible. Moreover, the CPSC General Counsel issued an advisory opinion that interprets the rule to apply retroactively to items in inventory on the date of enforcement (this same interpretation applies to the lead paint ban).[6]After notice and a hearing, the CPSC may exclude specific products and material if it determines that there will be no adverse impact on public health or safety, and the result would not lead to the absorption of any lead into the human body, given the normal and reasonably foreseeable use and abuse of such a product by a child. The CPSIA also allows for the exclusion of certain inaccessible component parts and electronic devices if certain criteria are met.
- A more stringent lead paint ban. Starting August 14, 2009, § 101 of the CPSIA also decreases the permissible amount of lead in paint from .06 percent to .009 percent. This ban applies to painted items such as furniture.[7]
- A prohibition on certain products containing phthalates. On February 10, 2009, pursuant to § 108, no one may import children’s toys or child care articles that contain more than 0.1 percent of certain phthalates (i.e., DEHP, DBP or BBP). Additionally, on the same date, the CPSIA places an interim ban on any toys and child care articles that can be placed in a child’s mouth that may contain more than 0.1 percent of another set of phthalates (i.e., DINP, DIDP or DnOP). A recent court ruling clarified that this ban also applies retroactively to items in inventory, despite the CPSC General Counsel’s advisory opinion that it did not.[8] (See National Resource Defense Council v. U.S. Consumer Product Safety Commission, No. 08 Civ. 10507 (S.D.N.Y. Feb. 5, 2009))
- New standards for toy safety and cribs. On February 10, 2009, § 106 of the law requires that toys meet the ASTM International Standard F963-07 as it existed on August 14, 2008. Per §104, the law also puts in place new safety standards for cribs, as well as other requirements for durable infant and toddler products.
Testing and Certification Requirements
Under §102 of the CPSIA, manufacturers (including importers) must now issue a general conformity certification for all imported products subject to any rule, ban, standard or regulation enforced by the CPSC when that product enters the country for consumption or warehousing.[9] This law expands the former requirement, which only required certification for a limited number of consumer products. These certificates must state that the product is in compliance with consumer product safety rules based on a test of each product or the existence of a reasonable testing program, and must also identify all of the regulations that apply to the product.
In addition, when importing a children’s product, § 102 of the CPSIA requires that the importer conduct third-party testing. The importer must submit a sample to an accredited third-party conformity assessment body and then, based on this testing, issue a certification that the product complies with the applicable consumer product safety rules. A separate certificate can be used for each applicable rule, or a combined certificate, which identifies each applicable rule and states that the product complies, will also suffice.
This requirement becomes effective on a rolling basis 90 days after the publication of the testing accreditation criteria for particular children’s products. Third-party testing and certification are already required for lead paint, cribs and pacifiers and will soon come into effect for items such as children’s metal jewelry and small parts.[10] As mentioned above, the CPSC has decided to stay enforcement of testing and certification requirements for the standards that go into effect on February 10, 2009.[11] Therefore, importers are not required to test or certify to the new lead content limits, phthalate content limits or mandatory toy standards until February 10, 2010. However, the underlying standards are still enforceable, and some testing and certification standards are still in effect (e.g., the lead paint rule, crib and pacifier standards).
In any case, both of these types of certificates must, in addition to others, include the following information in legible English—
- the identity of the product and the product safety regulation or statutory requirement to which it is being certified
- the identity of the issuer and, in the case of children’s products, the conformity assessment body
- the date and place of manufacture and testing
- each relevant party’s name and full contact information.[12]
These certificates must accompany the product or shipment, and each distributor and retailer must receive a copy of the certificate. The implementing regulations state that an electronic certificate “accompanies” a product if it can be reasonably accessed using information on or accompanying the product or shipment.[13] The CPSC gives a World Wide Web URL as an example of acceptable information, but other electronic means could suffice.[14] This information also satisfies “furnishing” of the certificate to distributors and retailers.
The importer must also ensure that certification is made prior to the arrival of the shipment into U.S. domestic commerce. [15] Furthermore, while any entity may maintain the electronic certificate platforms and enter the requisite data, the importer remains liable for the accuracy, timeliness and completeness of the certificate information.[16]
Tracking Requirement
Beginning August 14, 2009, pursuant to § 130 of the CPSIA, an importer must ensure that a children’s product has tracking labels on the product itself and the packaging, if practicable. This labeling must allow the manufacturer to identify the location and date of production, as well as additional “cohort information.” It must also allow the ultimate purchaser to ascertain this same information, as well as the identity of the manufacturer or private labeler.
Enforcement and Penalties
Section 222 of the CPSIA mandates increased cooperation between the CPSC and Customs and Border Protection (CBP). This cooperation will include information sharing and the increased presence of CPSC personnel at ports and targeting centers. It also involves a partnership between the agencies to expand CBP’s Importer Self-Assessment Program to include a Product Safety Pilot.[17] This program is a voluntary approach to product safety compliance that provides participating companies with support and recognition.[18] Additionally, to enhance enforcement, § 202 of the CPSIA increases the number of employees in the CPSC.
If violations are detected, § 217 of the CPSIA has strengthened the sanctions which can be levied against importers. Civil fines are increased from $5,000 to $100,000 per infraction with a cap at $15 million. For those who knowingly and willingly violate consumer product safety laws, criminal penalties allow sanctions of up to five years in jail. A criminal violation could also include forfeiture of assets associated with the breach.
The CPSIA also has other punitive measures that can be enforced against importers. Under § 223, if imported products are refused admission into the United States, the products will be destroyed unless, upon application of the owner, consignee or importer or record, the secretary of the Treasury permits export of the product. If export is granted, the applicant must export the products within 90 days of approval. Section 212 of the law also establishes a public database that makes available adverse reactions to a consumer product, as provided by consumers, local or national officials, child care providers and medical professionals. This negative publicity could have serious impact on brand name integrity.
Conclusion
To best meet these new requirements, importers must take a proactive role to know the true nature of the goods that they are importing and to ensure that the goods are in compliance with the CPSIA and its implementing regulations. To achieve this certainty, an importer must build traceability and transparency into the supply chain. Importers should convince suppliers to maintain reputable quality control systems and industry certifications. They must also establish a testing and certifying program that meets these requirements. Otherwise, importers risk violating this new law and having their supply of imported goods disrupted.
[1] Pub. L. No.110-314, 122 Stat. 3016 (2008).
[2] 15 U.S.C § 2052(a)(2).
[3] Id. at (a)(11).
[4] 74 Fed. Reg. 6396 (Feb. 9, 2009).
[5] Id.
[6] Advisory Opinion, CPSC General Counsel, “Retroactive Application of the CPSIA to Inventory” (Sep. 12, 2008).
[7] 16 C.F.R. § 1301.1.
[8] Advisory Opinion, CPSC General Counsel, Letter to Arent Fox LLP, (Nov. 17, 2008).
[9] 15 U.S.C. § 2063.
[10] 73 Fed. Reg. 54564, (Sep. 22, 2008); 73 Fed. Reg. 62965 (Oct. 22, 2008); 73 Fed. Reg. 67838 (Nov. 17, 2008); 73 Fed. Reg. 78331 (Dec. 22, 2008).
[11] 74 Fed. Reg. 6396 (Feb. 9, 2009).
[12] See 16 C.F.R. § 1110.11.
[13] 73 Fed. Reg. 68328 (Nov. 18, 2008).
[14] Id.
[15] Id.
[16] 16 C.F.R. § 1110.15.
[17] 73 Fed. Reg. 64356 (Oct. 29, 2008).
[18]Id.
CONTACT INFORMATION If you have questions about this alert, please contact:
|